Understanding Welding Positions: Flat, Horizontal, Vertical, and Overhead
Nov 20, 2023
Introduction
Welding, an intricate fusion of science and craftsmanship, relies significantly on the understanding of diverse welding positions. These positions, namely flat, horizontal, vertical, and overhead, form the bedrock of welding techniques. In this exploration, we delve into the intricacies of each, unraveling the nuances that underpin precision in the welding craft.
Definition of Welding Positions
Welding positions, akin to a complex dance choreography, dictate the orientation of the welding joint concerning the ground. Each position demands a unique approach, presenting distinct challenges and opportunities. From the stability of the flat position to the demanding nature of overhead welding, comprehending these orientations is pivotal for any welder.
Importance of Knowing Welding Positions
Why does an adept understanding of welding positions matter? Consider it the compass guiding a welder through the labyrinth of metal joining. Proficiency in manipulating the torch, controlling the arc, and managing molten metal flow hinges on the welder's mastery of the welding position. Whether it be executing a flawless bead in a flat joint or navigating the complexities of welding overhead, the importance of this knowledge cannot be overstated.
Moreover, welding positions influence the structural integrity of the weld. A misjudged position can compromise the weld's strength and durability, leading to structural failures in critical applications. Beyond technical considerations, safety also underscores the significance of knowing welding positions. Adhering to proper positions mitigates the risks of accidents, ensuring a secure working environment for the welder and those in proximity.
In essence, welding positions encapsulate the language through which welders communicate with metal. They are the grammar and syntax of this metallurgical dialogue, determining whether the resulting weld is a harmonious composition or a discordant amalgamation of metal and intention. As we embark on a detailed exploration of flat, horizontal, vertical, and overhead welding positions, the intricate dance of fusion and precision shall unfold.
Flat Position Welding (1G or 1F)
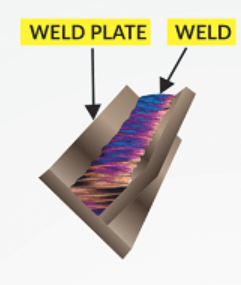
The flat position is often considered the starting point for many welders. In this position, the workpiece is located on a horizontal surface, such as a workbench or the floor. One significant advantage of the flat position is that welders are not working against gravity, making it the most accessible position. The welding torch or electrode is held at a 45-degree angle to the plate surface, ensuring even metal deposition into the joint.
Techniques for Flat Welding:
-
Maintain a consistent tip angle and flame position.
-
Employ a fluid motion for the weld puddle to evenly enter the joint.
-
Adjust parameters for the specific welding process being used.
Applications:
-
Suitable for all welding processes.
-
Easier to weld in due to gravity aiding in metal deposition.
Horizontal Position Welding (2F or 2G)
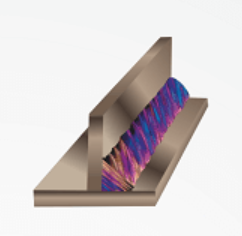
As the name suggests, the horizontal welding position involves the welding axis staying horizontal. In the case of 2F fillet welds, welding is done on the upper side of horizontal and vertical surfaces, while 2G groove welds involve welding on the vertical plane with the face of the weld lying on that plane. Horizontal welding presents additional challenges compared to the flat position, as the weld puddle can sag if the molten metal is too hot.
Techniques for Horizontal Welding:
-
Favor the top edge of the joint to prevent excessive sagging.
-
Adjust parameters to prevent the weld puddle from becoming too fluid.
-
Practice and refine techniques due to the out-of-position nature of horizontal welding.
Applications:
-
Similar to flat welding but requires more practice.
-
Common in various industries for welding joints that cannot be positioned horizontally.
Vertical Position Welding (3F or 3G)
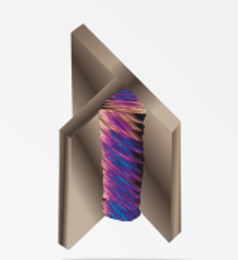
In vertical welding, the axis of the weld remains vertical, either moving up or down. The workpiece and the weld are perpendicular or almost perpendicular, introducing new challenges, such as molten metal flowing downward and accumulating. The 3F position is for vertical fillet welding, while 3G is for vertical groove welding.
Techniques for Vertical Welding:
-
Use a zigzag, upside-down, or triangular motion to manipulate the weld puddle.
-
Adjust parameters to account for the effects of gravity on the weld puddle.
-
Consider whether the weld will be done vertically up or down, with vertical up being more common for thicker materials.
Applications:
-
Widely used in fabricating and installing pipes and pipelines.
-
Requires careful attention to technique and parameters to avoid defects.
Overhead Position Welding (4F or 4G)
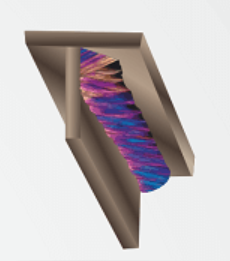
Welding in the overhead position involves working from the lower surface of the joint. This challenging position requires extra caution, as the metal deposited can sag, leading to higher crowns in the beads. Overhead welding is often necessary when the workpiece is fixed and cannot be moved.
Techniques for Overhead Welding:
-
Position the torch at a 45-degree angle.
-
Keep the molten metal puddle small to avoid excessive sagging.
-
Use techniques similar to vertical welding for puddle manipulation.
Applications:
-
Essential when the workpiece cannot be repositioned.
-
Requires additional safety measures due to falling sparks.
-
(This welding postion is quite dangerous while welding, please wear protective gear, such as a Helmet RLM-800 that combines performance and quality. No matter what job you are doing, safety always comes first.)


Common Mistakes in Welding Positions
Inadequate Preparation
The welding arena is unforgiving to those who neglect meticulous preparation. Inadequate cleaning of the joint, lax fixture setup, or underestimating the importance of a pristine workspace serves as a breeding ground for subpar welds. Attention to detail in preparation is the linchpin for achieving welds of the highest caliber.
Incorrect Electrode/Arc Placement
Precision in welding is an orchestration of electrode and arc movements. A misjudgment in the placement of the electrode or the trajectory of the arc can lead to irregular welds, insufficient penetration, and a subsequent need for rectification. The key lies in understanding the optimal placement for each welding position, akin to a conductor directing a symphony.
Insufficient Heat Control
The delicate equilibrium of welding positions relies heavily on the control of heat. A surplus can result in material distortion, while insufficient heat may yield welds with inadequate strength. Navigating this thermal tightrope is a challenge for many welders, requiring a meticulous balance for a flawless welding performance.
Thorough Pre-Welding Inspection and Preparation
Diligence in inspecting and preparing the welding environment is not a mere formality but a prerequisite for success. A clean, well-prepared joint ensures an optimal canvas for the welder's artistry, minimizing the risk of contamination and maximizing the integrity of the final weld.
Welding Positions in Different Industries
Construction and Structural Welding Positions

In the domain of construction, welding positions are the architects of stability. The flat welding position, akin to a craftsman laying a foundation, seamlessly unites horizontal elements, giving birth to the skeletal framework of buildings. Horizontal welding positions emerge as silent fortifiers, weaving lateral strength into beams and joints that bear the structural load. The vertical welding position, a choreographer of elevation, erects the pillars that reach for the sky. Together, they construct edifices that stand as tributes to the precision and strength inherent in the welding positions within the construction industry.
Aerospace Welding Positions

High above the clouds, the art of aerospace engineering relies on the dance of welding positions with unmatched precision. Flat welding positions, akin to sculptors of the sky, craft aerodynamic wings that navigate the boundless expanse. Horizontal welding positions seamlessly join fuselage components, ensuring the structural resilience essential for soaring through the heavens. Vertical welding positions contribute their grace to intricate components, adding strength to the aerial ballet. The overhead welding position, a virtuoso performance, assembles components defying both gravity and earthly limitations. Aerospace welding positions create vessels that not only traverse the skies but exemplify the synergy of technical finesse and aeronautical elegance.
Automotive Welding Positions
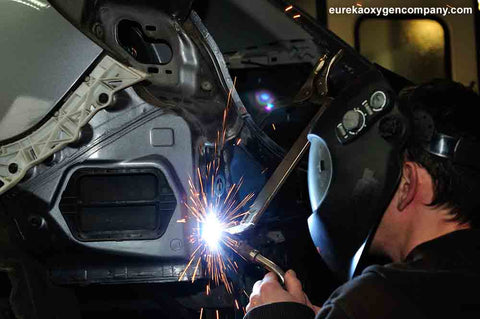
In the realm of automobiles, welding positions shape the vessels of speed and sophistication. The flat welding position, a conductor of stability, welds the chassis components, forming a robust foundation for automotive excellence. Horizontal welding positions, the artisans of lateral strength, join components that define the vehicle's body, marrying form with function. Vertical welding positions fortify pillars and supports, contributing to the structural integrity of the vehicle on the open road. Automotive welding positions, like skilled painters, blend power and aesthetics, creating vehicles that traverse roads with both prowess and style.
Shipbuilding and Marine Welding Positions
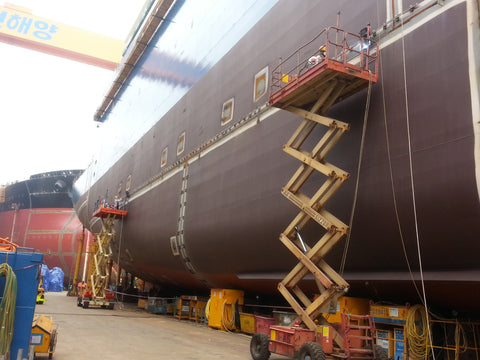
Beneath the expansive horizon of the ocean, welding positions become the architects of maritime prowess. Flat welding positions, as maritime sculptors, construct the watertight hull, ensuring the vessel's buoyancy in the undulating seas. Horizontal welding positions, like skilled navigators, link lateral components such as bulkheads and decks, contributing to the vessel's structural resilience against the relentless waves. Vertical welding positions, the choreographers of stature, elevate masts and supports, defining the vessel's presence on the water. The overhead welding position, a seafaring virtuoso, assembles components beneath the waterline, completing the maritime tableau. Shipbuilding welding positions create vessels that sail as silent symphonies, conquering the vastness of the open sea.
Conclusion
Understanding welding positions is fundamental for welders at all skill levels. Each position comes with its challenges and requires specific techniques and parameter adjustments. Whether you're working in the flat, horizontal, vertical, or overhead position, prioritizing safety is paramount. By combining technical expertise with a commitment to safety, welders can achieve consistent and high-quality welds across various applications.