A Comprehensive Guide to Learning Pipeline Welding Techniques and Technologies
Dec 20, 2023
The pipeline welding industry in the United States is a dynamic and essential sector, employing a significant workforce to ensure the integrity and reliability of pipelines across the nation. Let's explore the fascinating world of pipeline welding, exploring its intricacies, challenges, and the rewarding career it offers.
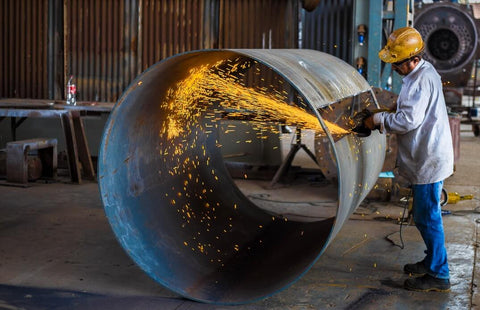
Industry Insights: Statistics and Trends
Before we embark on the journey of understanding pipeline welding, let's take a glance at some key statistics that define this industry. According to recent research, there are over 281,000 pipe welders currently employed in the United States, with an average age of 40 years. While the majority (96.0%) are men, women represent 4.0% of the workforce. Notably, the demand for pipe welders is particularly high in Raleigh, NC, showcasing the industry's regional variations.
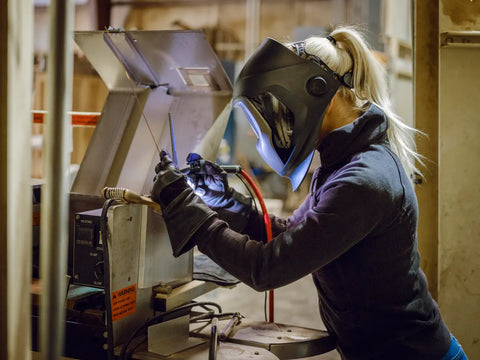
Regarding compensation, North Kingstown, RI, leads the charts with an annual average wage of $57,373. The average salary of a pipeline welder in the U.S. is $44,722 per year, with experienced professionals earning $57,000 and above. Despite the gender gap, it's encouraging to note that, in 2022, female pipe welders earned 85% of what their male counterparts earned. As we explore the pipeline welding domain, these statistics provide a backdrop to the robust and evolving nature of the industry.
Learning the Art of Pipeline Welding
Pipeline welding stands at the intersection of skill, precision, and versatility, where the mastery of diverse welding techniques is paramount. Aspiring welders enter into a realm that extends beyond mere technical proficiency; it demands a profound understanding of materials, welding processes, and the unique challenges presented by pipeline installations.
Diverse Arc Welding Techniques:
The foundation of pipeline welding lies in the mastery of various arc welding techniques, each tailored to suit specific applications and materials. These techniques form the backbone of a welder's skill set:
Shielded Metal Arc Welding (SMAW):
Commonly known as stick welding, SMAW employs a stick-shaped electrode to create an electric arc that melts the metal during welding.
This versatile technique finds its application in joining hard-to-reach areas and materials of varying thicknesses, including carbon steel, stainless steel, and cast iron.
The welder's control over the electrode angle and movement determines the size and shape of the weld.
Gas Metal Arc Welding (GMAW):
GMAW, or MIG welding, utilizes a continuous wire electrode to weld metal. The electric arc formed between the electrode and the workpiece heats the metal, facilitating the joining process.
Ideal for welding pipes due to its ease of use and high-quality weld production, GMAW requires a welding machine, a welding gun, a wire electrode, and shielding gas.
The process involves feeding the wire electrode into the weld pool and moving the welding gun in a circular motion to create a seamless weld.
Flux-Cored Arc Welding (FCAW):
FCAW is an exceptional technique using a tubular electrode filled with flux, offering protection against atmospheric contamination and enhancing weld quality.
Versatile enough to weld materials like carbon steel, low alloy, and stainless steel, FCAW is particularly advantageous for thicker-walled pipes and applications requiring higher deposition rates.
Submerged Arc Welding (SAW):
SAW is commonly employed for welding low and high-alloy steel and carbon steel pipes. It involves creating an arc submerged beneath a flux layer, shielding the weld pool from atmospheric contamination.
Known for its efficiency and productivity, SAW produces high-quality welds with minimal operator intervention, making it a preferred choice for pipe welding applications.
Tungsten Inert Gas (TIG) Welding:
Also known as Gas Tungsten Arc Welding (GTAW), TIG welding is used in pipe welding to join stainless steel, aluminum, and other non-ferrous materials.
Employing a non-consumable tungsten electrode, TIG welding creates an arc with the workpiece, melting both the electrode and base metal to form a durable weld.
TIG welding's precision and ability to produce clean welds with minimal heat distortion make it suitable for thin-walled pipes.
Which welding method is right for you? Which one do you want to choose?
No need to worry, the brand new Upgraded SD-4050Pro(2024) welder and cutter is on sale now, with powerful ten-in-one functions, upgraded LCD screen, pulse TIG, foot pedal \ spool gun supported, dual fan cooling, etc.
The Learning Journey:
Aspiring pipeline welders take on a comprehensive learning journey that goes beyond theoretical knowledge. Hands-on experience often gained through apprenticeships or vocational training programs, is integral to honing the craft. Understanding the nuances of each welding technique, practicing in simulated environments, and mastering the art of adapting to diverse materials and working conditions define the learning curve.
Continuous Skill Refinement:
Pipeline welding is not a static skill; it requires continuous adaptation and refinement. Technological advancements, changes in materials, and evolving industry standards necessitate a commitment to lifelong learning. Welders engage in ongoing training and professional development to stay abreast of the latest techniques, equipment, and safety protocols.
Why is Pipeline Welding Hard?
Mastering pipeline welding is a challenging feat, and several factors contribute to the complexity of this craft. One primary challenge is the diversity of materials encountered in pipeline welding, ranging from carbon steel and stainless steel to cast iron. Welders must adapt their techniques to suit the specific properties of each material, showcasing the need for versatility in their skill set.

The nature of pipeline installations, often in challenging environments and varying weather conditions, adds another layer of complexity. Welders must contend with tight spaces, adverse weather, and sometimes challenging access points, demanding a high level of adaptability and problem-solving skills.
Vertical Down vs. Vertical Up Welding
Within the realm of pipeline welding, the choice between vertical down and vertical up welding techniques holds significance.
Vertical down welding involves depositing the weld from top to bottom, allowing for faster travel speeds and increased efficiency. On the other hand, vertical up welding requires depositing the weld from bottom to top, often chosen for its ability to penetrate deeper into the base metal.
The decision between these techniques depends on factors such as pipe diameter, wall thickness, and the specific requirements of the welding project. Welders must possess a nuanced understanding of these techniques to execute precise and high-quality welds.
Pipe Welding Positions
Understanding and mastering pipe welding positions is crucial for pipeline welders. The four primary pipe welding positions are:
- PA (1G)
- PC (2G)
- PF (5G)
- H-L045 (6G)
Each position presents its own set of challenges, with PA being the easiest to master and H-L045 considered the most difficult.
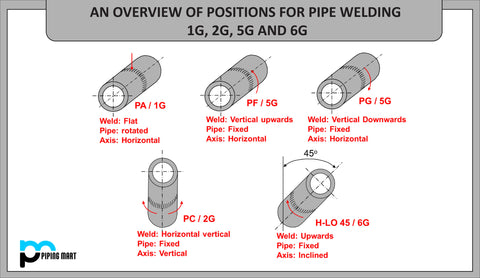
Welders undergo certification for each position, ensuring that they are well-equipped to handle the varying demands of pipe welding. Safety remains paramount, and adherence to certification standards ensures a secure work environment.
Pipeline Welding As a Career
Taking on a career in pipeline welding is not just a job; it's a journey filled with challenges and rewards. The challenges are apparent – from mastering diverse welding techniques to navigating complex working environments. However, the rewards are equally compelling.
Challenges
Versatility: Pipeline welders must adapt to working with different materials, requiring a deep understanding of each material's welding nuances.
Environmental Factors: Working outdoors, often in adverse conditions, demands resilience and adaptability.
Precision: The need for precise welds in varied positions adds an element of complexity, necessitating continuous skill refinement.
Rewards
Job Security: The constant demand for pipeline infrastructure ensures a stable job market for skilled welders.
Competitive Salaries: With experience and expertise, pipeline welders can enjoy competitive salaries.
Professional Growth: Continuous learning and skill development are inherent to the profession, offering avenues for career advancement.

Conclusion:
Pipeline welding is a profession that demands commitment, skill, and a passion for precision. The industry's growth, coupled with the essential role pipelines play in infrastructure, makes it a compelling career choice for those ready to embrace its challenges and reap the rewards. Aspiring welders should consider not only the technical aspects of the craft but also the resilience and adaptability required to thrive in this dynamic field.
1 comment
The blog provides a detailed overview of pipeline welding techniques and technologies, covering the key methods used for welding pipelines such as SMAW (Shielded Metal Arc Welding), GTAW (Gas Tungsten Arc Welding), and FCAW (Flux-Cored Arc Welding). It highlights the importance of precision and quality in pipeline welding to ensure strong, leak-proof joints. The guide also emphasizes the role of modern technologies and practices in enhancing the efficiency and safety of pipeline welding operations.